- Gate valves are critical components in numerous industrial applications, from oil and gas pipelines to water treatment facilities. Understanding the various gate valve parts and their functions is essential for proper selection, installation, and maintenance. This comprehensive guide breaks down each component, explores material considerations, and provides valuable maintenance insights to help you maximize the performance and lifespan of your gate valves.
What Are Gate Valves and Their Applications:
- Gate valves are linear motion valves that control flow by raising or lowering a gate (or wedge) perpendicular to the flow path. When fully open, gate valves provide minimal restriction to flow, making them ideal for applications where straight-line flow with minimal pressure drop is required.
- These valves are extensively used in industries where on/off control (rather than flow regulation) is needed. Their design allows for bidirectional flow and they can handle a wide range of pressures, temperatures, and media types depending on their construction materials.
- Gate valves are not recommended for throttling applications as partial opening can cause the gate and seat to erode quickly, leading to leakage when the valve is closed.
Common Applications of Gate Valves:
- Oil and gas transmission pipelines
- Water and wastewater treatment systems
- Power generation facilities
- Chemical processing plants
- Mining operations
- Pulp and paper manufacturing
- Food and beverage processing
- HVAC systems in large buildings
- Fire protection systems
- Marine and offshore applications
Core Components of Gate Valves:
- Understanding the function of each gate valve part is crucial for proper selection, maintenance, and troubleshooting. Let’s examine the key components that make up a typical gate valve.
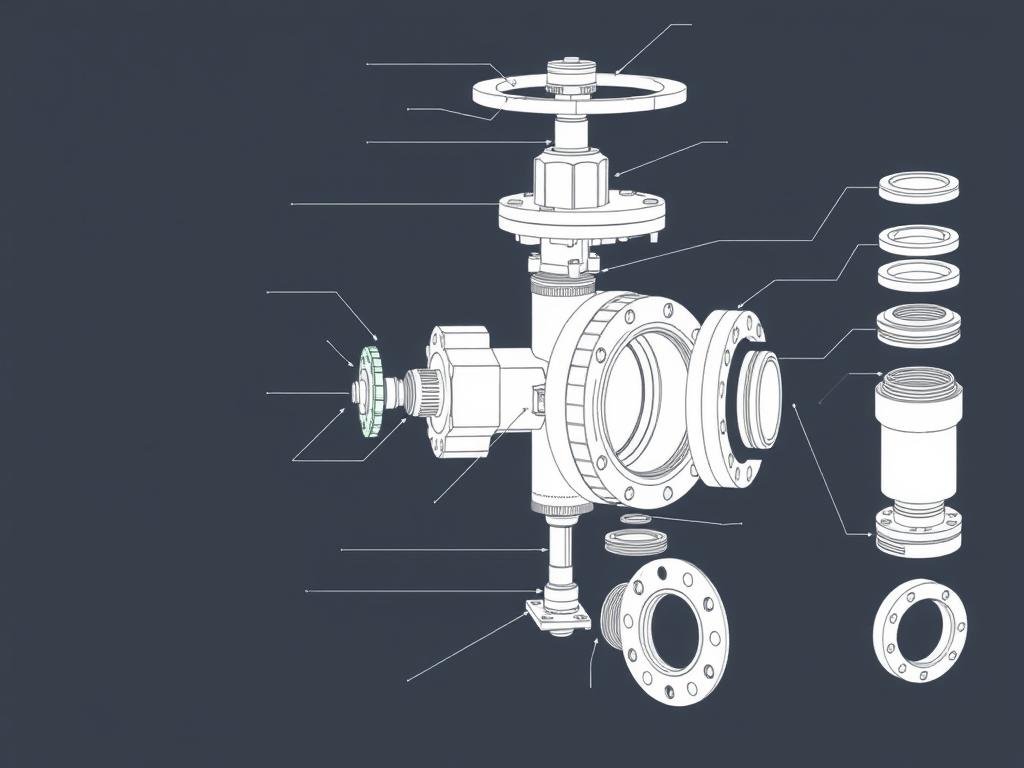
Valve Body: The Pressure-Retaining Shell:
The valve body is the primary pressure-containing component that houses all internal parts and connects to the piping system. It must withstand system pressure and temperature while providing structural support for the entire assembly.
Body Connection Types:
- Flanged connections: Most common in industrial applications, using standardized flange patterns
- Threaded connections: Typically used in smaller valves and lower pressure applications
- Butt-weld connections: Provide the strongest joint for high-pressure, high-temperature service
- Socket-weld connections: Common in smaller high-pressure applications
Body Designs:
- Cast bodies: Most common, economical for standard applications
- Forged bodies: Higher strength for severe service conditions
- Fabricated bodies: Custom-designed for special applications
- Split bodies: Allow for easier maintenance of internal components
Bonnet: The Access Cover:
The bonnet serves as a removable cover for the valve body, providing access to internal components for maintenance while containing the system pressure. Different bonnet designs are used based on pressure, temperature, and maintenance requirements.
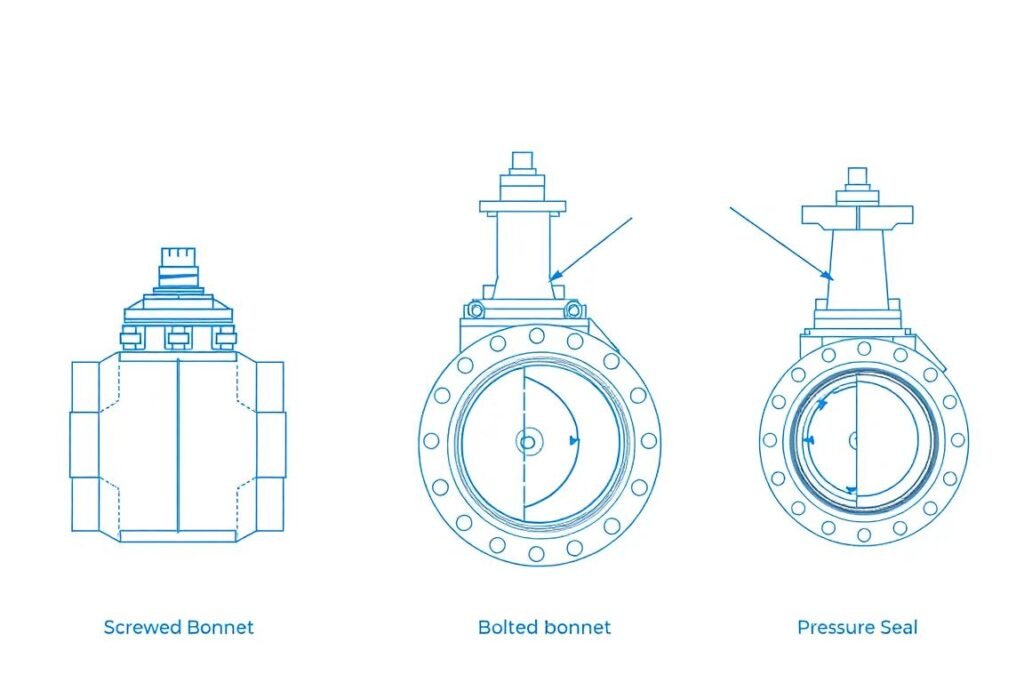
1). Screwed Bonnet:
- Threaded directly onto the valve body, these are economical and compact but limited to smaller sizes and lower pressures. Maintenance requires complete valve removal.
2). Bolted Bonnet:
- Attached to the body with bolts and a gasket, this is the most common design. It allows for easier maintenance and can handle higher pressures than screwed bonnets.
3). Pressure Seal Bonnet:
- Designed for high-pressure applications, this bonnet uses system pressure to enhance the seal. The higher the pressure, the tighter the seal becomes.
Stem: The Operating Mechanism:
- The stem connects the actuator (handwheel, gear, or powered operator) to the gate, converting rotational motion to linear motion. The stem design significantly impacts valve operation, maintenance requirements, and installation space needs.
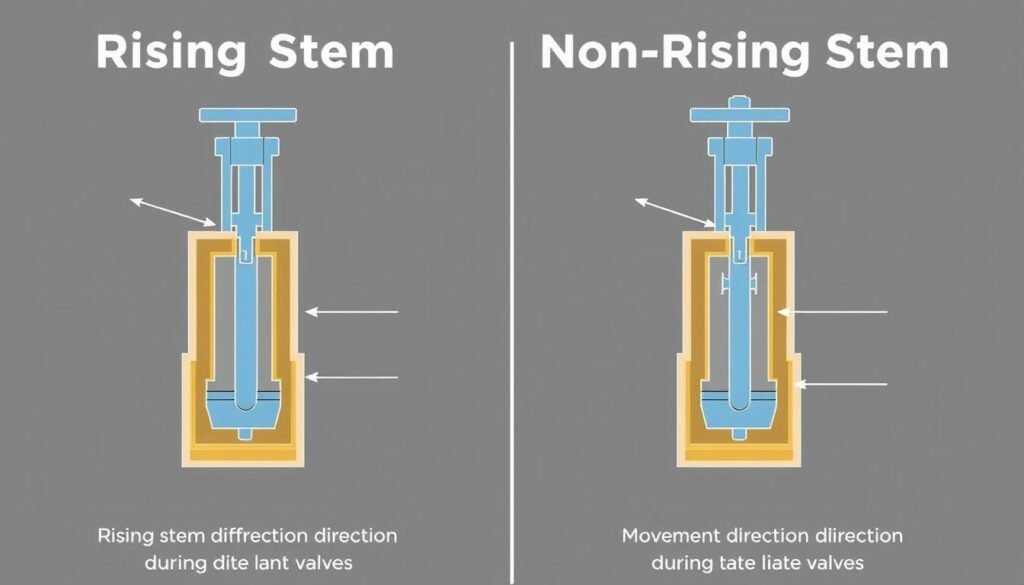
1). Rising Stem (OS&Y – Outside Screw and Yoke):
In rising stem designs, the stem moves upward as the valve opens. This provides a visual indication of valve position but requires vertical clearance for operation. The stem threads are located outside the flow media, reducing corrosion concerns.
- Visual position indication
- Threads protected from process media
- Easier maintenance of stem threads
- Requires more installation space
2). Non-Rising Stem (NRS):
In non-rising stem designs, the stem rotates but does not move vertically. The gate travels up the threaded portion of the stem. This design requires less vertical space but offers no visual indication of valve position.
- Compact installation profile
- Ideal for underground or limited-space applications
- No visual position indication
- Stem threads exposed to process media
Gate: The Flow Control Element:
- The gate is the movable barrier that controls flow through the valve. Different gate designs are used depending on the application, media type, and required sealing performance.
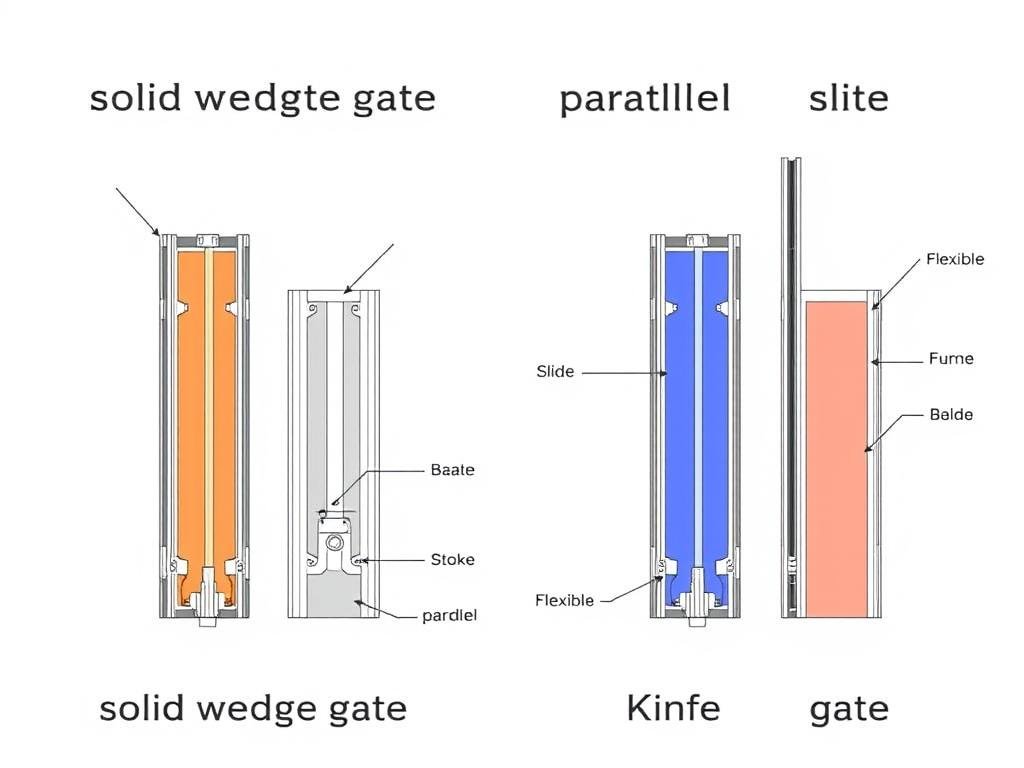
1). Solid Wedge Gate:
- A single-piece tapered disc that seats between angled seat surfaces. Most common design for general service applications.
2). Flexible Wedge Gate:
- Similar to solid wedge but with a groove cut into the center, allowing slight flexing to accommodate thermal expansion.
3). Parallel Slide Gate:
- Two parallel discs with a spreading mechanism that forces them against the seats when closing. Good for high-temperature applications.
4). Knife Gate:
- Thin, sharp-edged gate designed to cut through slurries and viscous fluids. Common in pulp, paper, and wastewater applications.
Seat: The Sealing Surface:
- The seat provides the sealing surface against which the gate closes. Seat design and material significantly impact valve sealing performance and longevity.
Seat Types
- Integral seats: Machined directly into the valve body
- Seat rings: Separate components inserted into the body
- Resilient seats: Soft materials for tight shutoff
- Metal seats: For high-temperature applications
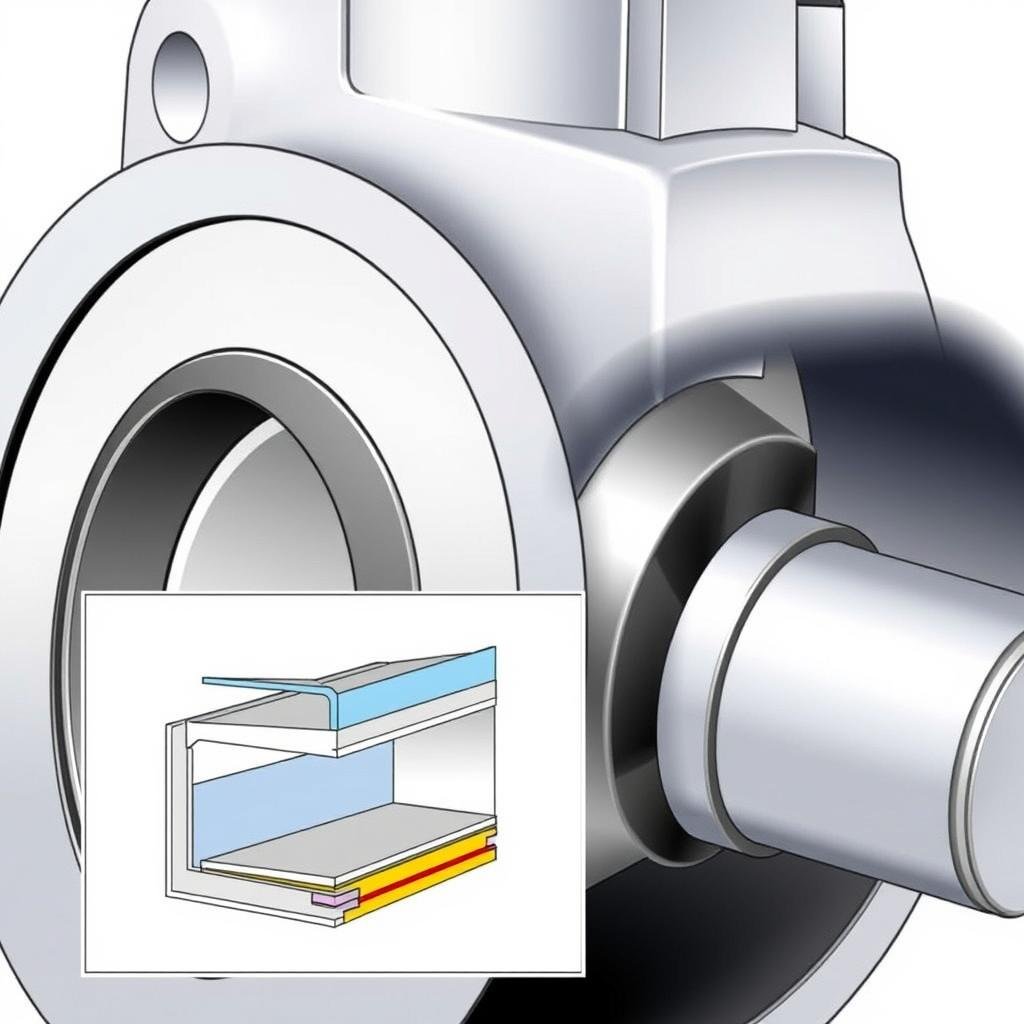
Additional Components:
1). Packing and Gland:
- The packing seals the stem where it passes through the bonnet, preventing leakage. The gland compresses the packing to maintain the seal. Proper packing adjustment is critical for leak-free operation and stem longevity.
2). Yoke:
- In OS&Y designs, the yoke supports the stem nut and provides the structure against which the stem operates. It must be strong enough to withstand the forces required to operate the valve.
3). Handwheel or Actuator:
- The device used to operate the valve. Manual valves use handwheels, while automated valves may use electric, pneumatic, or hydraulic actuators depending on application requirements.
Material Considerations for Gate Valve Parts:
- The materials used in gate valve construction determine its suitability for specific applications, media compatibility, pressure-temperature ratings, and service life. Selecting appropriate materials is crucial for safe and reliable valve operation.
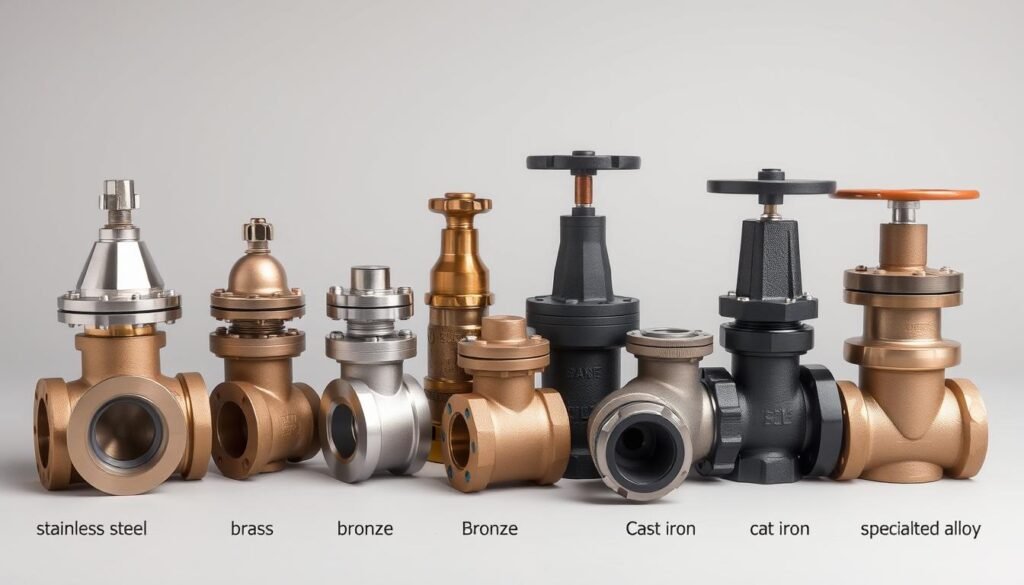
Component | Common Materials | Application Considerations |
Body & Bonnet | Cast Iron, Carbon Steel, Stainless Steel, Bronze, Alloy Steels | Must withstand system pressure, temperature, and media corrosiveness |
Gate | Carbon Steel, Stainless Steel, Bronze, Nickel Alloys | Requires strength, wear resistance, and compatibility with process media |
Stem | Stainless Steel, Bronze, Monel, Inconel | Needs tensile strength, corrosion resistance, and good thread properties |
Seats | Bronze, Stainless Steel, Stellite (hardfacing), PTFE, PEEK | Must provide good sealing properties and wear resistance |
Packing | PTFE, Graphite, EPDM, Kevlar, Flexible Graphite | Needs to maintain seal under pressure while allowing stem movement |
Gaskets | Compressed Fiber, PTFE, Spiral Wound, Metal Jacketed | Must maintain body-bonnet seal under varying conditions |
Material Selection Factors:
1). Process Compatibility:
- Materials must be compatible with the process media to prevent corrosion, erosion, or chemical attack that could lead to premature failure. Consider chemical compatibility, pH levels, and presence of abrasive particles.
2). Temperature Range:
- Materials must maintain their mechanical properties throughout the operating temperature range. High temperatures can reduce strength and cause creep, while low temperatures may cause embrittlement in some materials.
3). Pressure Rating:
- Materials must withstand system pressure with an appropriate safety factor. Pressure ratings decrease as temperature increases, following standardized pressure-temperature ratings.
Gate Valve Actuation Methods:
- Gate valves can be operated manually or with powered actuators depending on application requirements, valve size, operating frequency, and accessibility considerations.
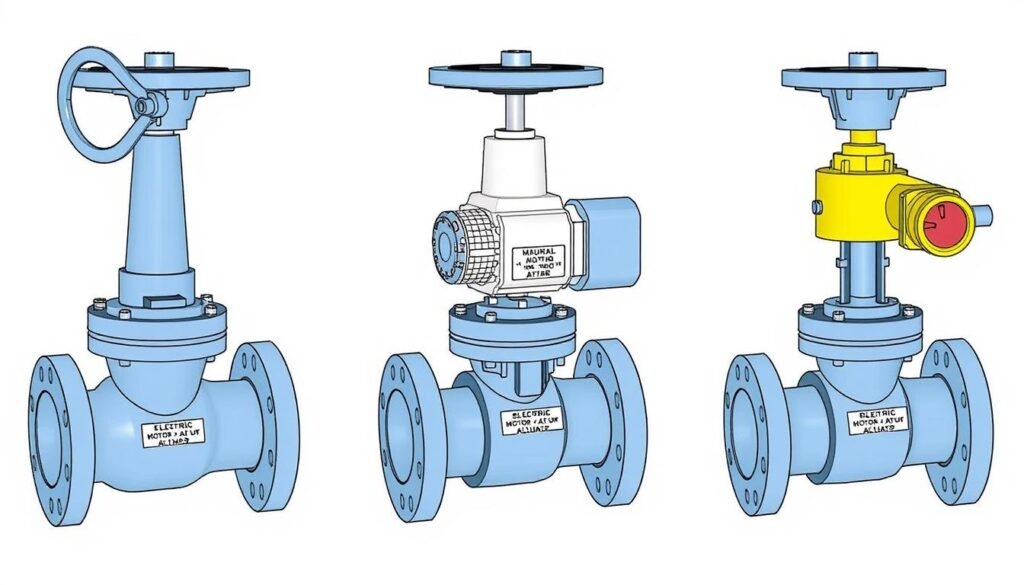
1). Manual Operation:
- Using handwheels or levers, manual operation is simple and reliable but requires physical effort. Larger valves may use gearboxes to reduce required operating torque. Manual valves are ideal for infrequently operated applications or where power is unavailable.
2). Electric Actuation:
- Electric motors provide precise control and can be integrated with control systems. They offer position feedback, torque limiting, and remote operation capabilities. Electric actuators are ideal for remote locations with available power.
3). Pneumatic/Hydraulic Actuation:
- Using compressed air or hydraulic pressure, these actuators provide fast operation and are intrinsically safe for hazardous areas. They’re ideal for emergency shutdown applications or where rapid operation is required.
Gate Valve Maintenance and Troubleshooting:
- Proper maintenance is essential for ensuring reliable gate valve operation and extending service life. Regular inspection and preventive maintenance can identify potential issues before they lead to valve failure.
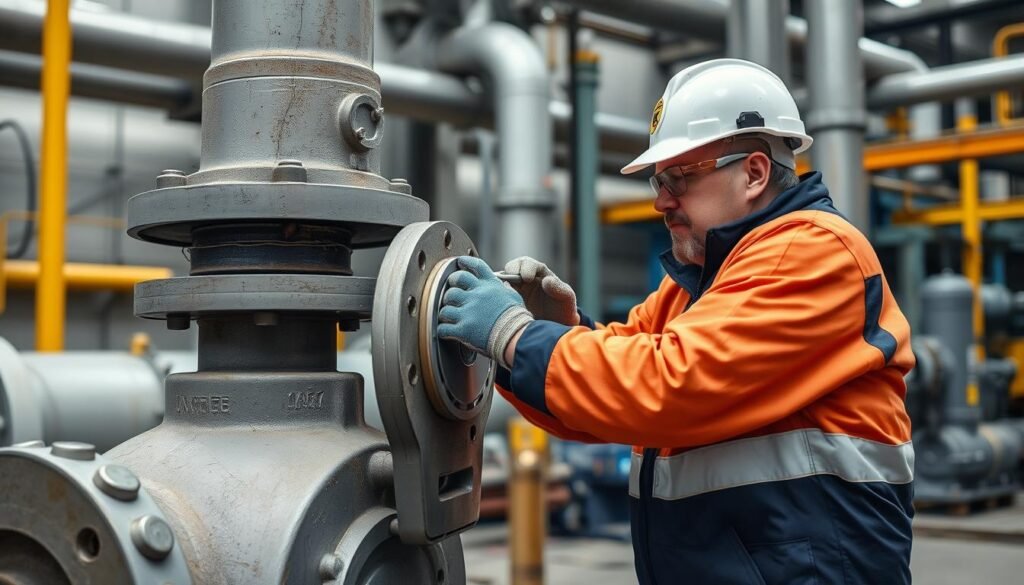
Common Maintenance Procedures:
Packing Adjustment and Replacement:
Stem packing is a wear item that requires periodic adjustment and eventual replacement. Signs of packing wear include leakage around the stem and difficult valve operation.
- Tighten packing gland nuts evenly in small increments
- Avoid over-tightening which can cause excessive stem friction
- If adjustment doesn’t stop leakage, replace packing
- Ensure proper packing material for the application
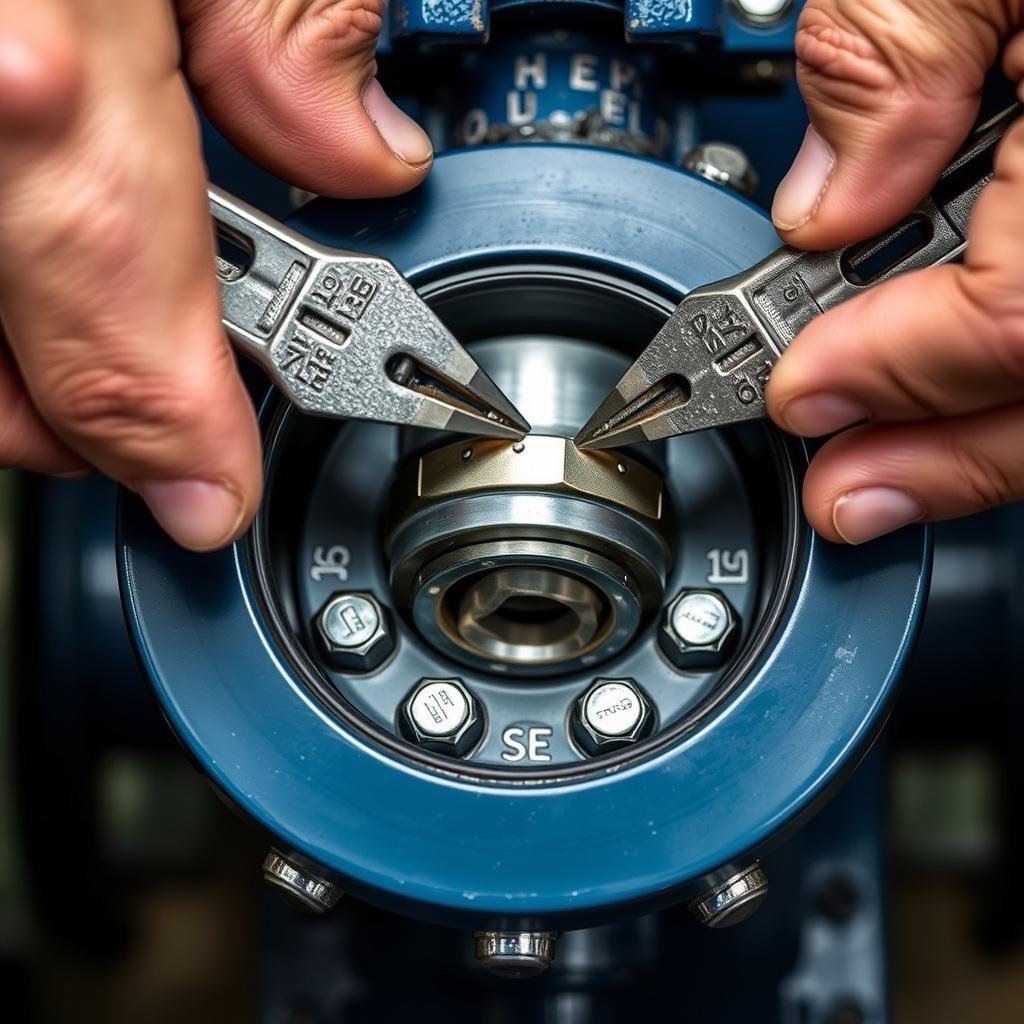
Troubleshooting Common Gate Valve Issues:
Problem | Possible Causes | Recommended Actions |
Leakage through closed valve | Worn or damaged seats, debris between gate and seat, gate not fully closed | Inspect and clean seats, check for proper gate alignment, repair or replace damaged components |
Stem leakage | Worn packing, loose gland, damaged stem surface | Adjust or replace packing, inspect stem for damage, replace stem if necessary |
Difficult operation | Over-tightened packing, stem damage, corrosion, misalignment | Adjust packing, lubricate stem, check for binding or misalignment |
Body-bonnet leakage | Loose bolting, damaged gasket, uneven bolt torque | Check bolt torque, replace gasket, ensure proper bolt tightening sequence |
Maintenance Best Practices:
- Establish regular inspection schedules based on service severity
- Document valve maintenance history and observed issues
- Use proper tools and techniques to avoid component damage
- Follow manufacturer’s recommendations for maintenance procedures
- Keep spare parts inventory for critical valves to minimize downtime
Gate Valve Selection Guide:
- Selecting the right gate valve involves considering multiple factors to ensure it meets application requirements and provides reliable service. This guide outlines key considerations for proper gate valve selection.
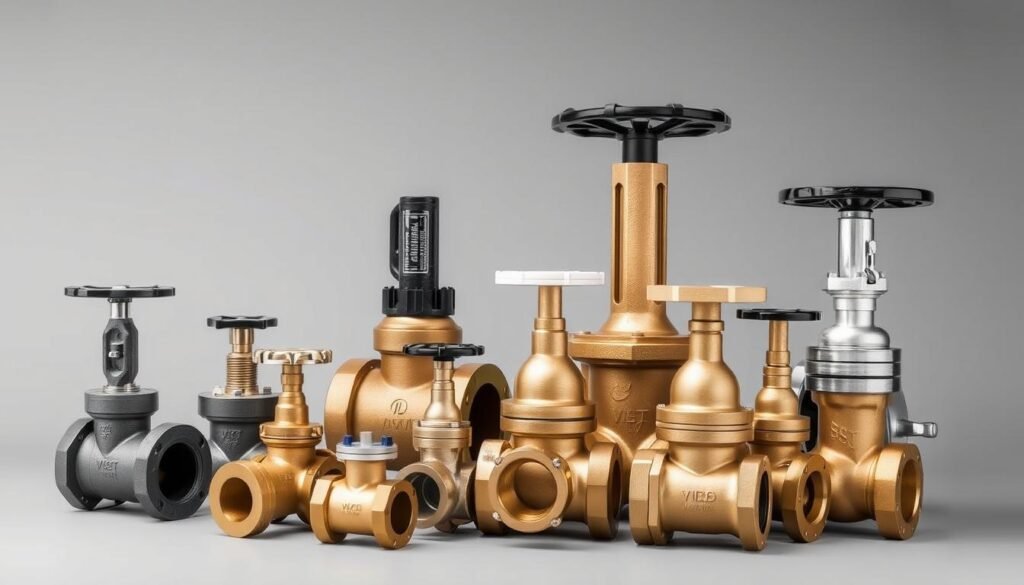
Key Selection Factors:
Service Conditions:
- Process media (liquid, gas, slurry)
- Operating pressure and temperature
- Corrosiveness and abrasiveness
- Flow characteristics
Valve Specifications:
- Size and connection type
- Pressure class rating
- Body and trim materials
- Stem type (rising vs. non-rising)
Operational Requirements:
- Frequency of operation
- Actuation method
- Installation space constraints
- Maintenance accessibility
Gate Valve Applications Across Industries:
- Gate valves serve critical functions across numerous industries, with specific designs and materials tailored to each application’s unique requirements.
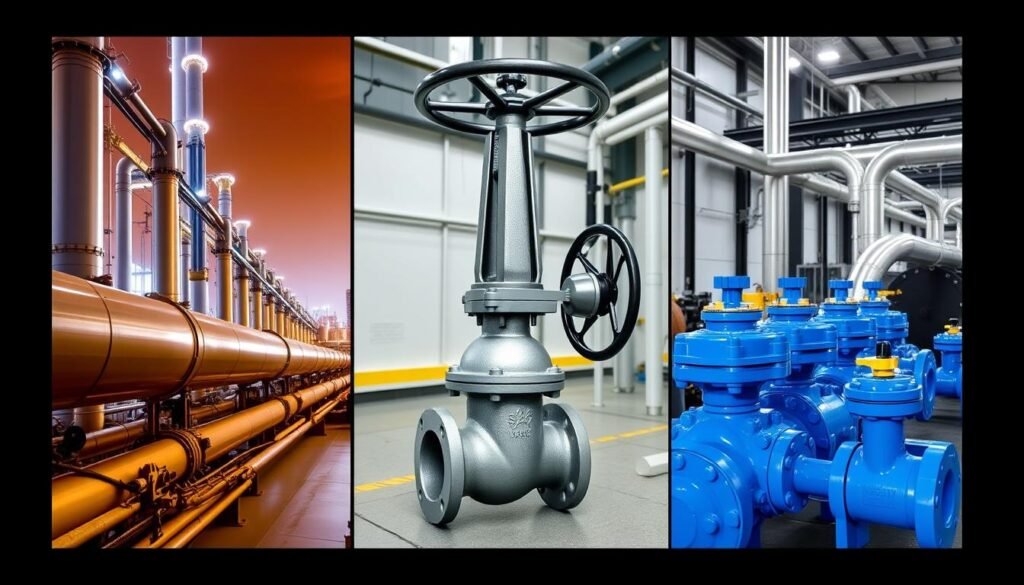
1). Oil and Gas:
- In upstream, midstream, and downstream operations, gate valves control flow in wellheads, pipelines, refineries, and distribution systems. These applications often require fire-safe designs, high-pressure ratings, and corrosion-resistant materials.
2). Water and Wastewater:
- Municipal water systems use gate valves for isolation in distribution networks, treatment plants, and pump stations. These applications typically use resilient-seated gates for bubble-tight shutoff and corrosion-resistant materials.
3). Power Generation:
- Power plants use gate valves in cooling water systems, steam lines, and feedwater systems. These applications often require high-temperature materials, pressure seal bonnets, and specialized trim for erosion resistance.
4). Chemical Processing:
- Chemical plants use gate valves for process isolation where tight shutoff is required. These applications often need specialized materials for chemical compatibility and may require bellows seals for hazardous media.
5). Mining:
- Mining operations use gate valves in slurry transport, water management, and processing systems. These applications typically require abrasion-resistant materials and knife gate designs for handling solids-laden fluids.
6). Pulp and Paper:
- Pulp and paper mills use gate valves in stock preparation, chemical handling, and water systems. These applications often use knife gate valves for handling pulp slurries and corrosion-resistant materials for chemical service.
Standards and Certifications for Gate Valves:
- Gate valves are manufactured according to various industry standards that govern design, materials, testing, and performance requirements. Understanding these standards is important for ensuring proper valve selection and compliance with industry regulations.
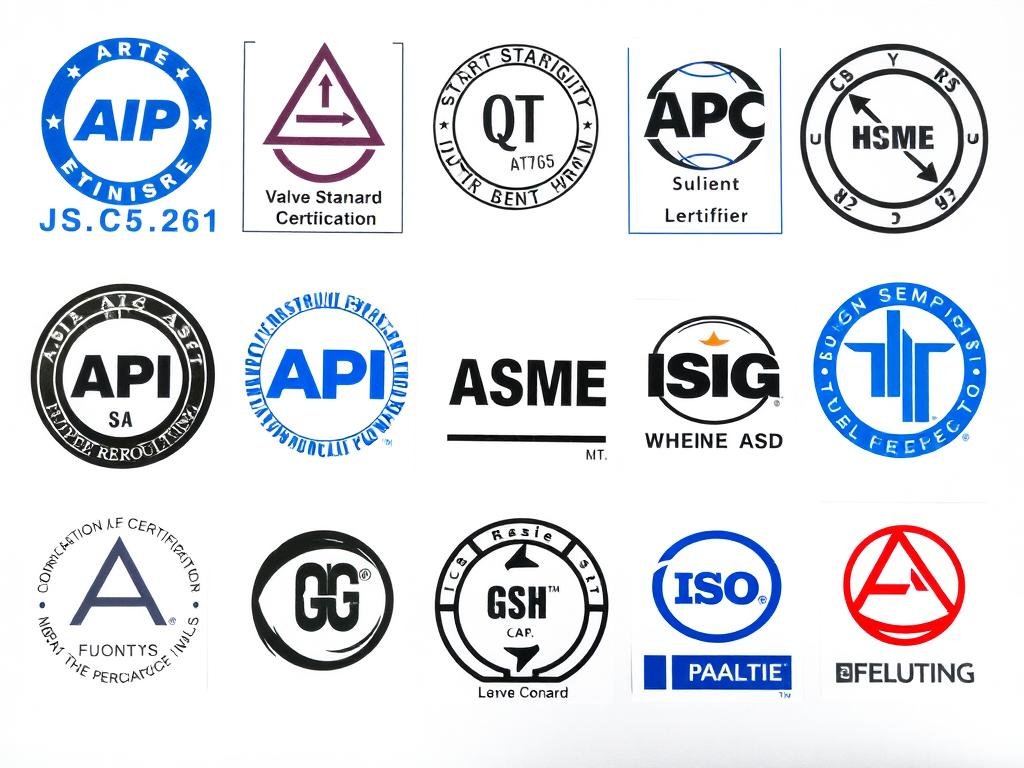
Key Industry Standards:
Design and Manufacturing Standards:
- API 600: Steel gate valves – flanged and butt-welding ends
- API 602: Steel gate valves – small forged, threaded and welding end
- API 603: Corrosion-resistant gate valves
- ASME B16.34: Valves – flanged, threaded, and welding end
- MSS SP-70: Cast iron gate valves
- MSS SP-80: Bronze gate valves
Testing and Performance Standards:
- API 598: Valve inspection and testing
- API 6D: Pipeline valves
- ISO 5208: Industrial valves – pressure testing
- MSS SP-61: Pressure testing of valves
- ASME B16.10: Face-to-face and end-to-end dimensions
- ASME B16.5: Pipe flanges and flanged fittings
Conclusion: Ensuring Reliable Gate Valve Performance:
- Gate valves are critical components in numerous industrial applications, providing reliable flow control when properly selected, installed, and maintained. Understanding the various gate valve parts, their functions, and material considerations is essential for maximizing valve performance and service life.
- Regular inspection and maintenance of gate valve components—including the body, bonnet, stem, gate, seats, and packing—helps prevent unexpected failures and extends operational life. By following industry best practices for selection, installation, and maintenance, you can ensure your gate valves provide reliable service in even the most demanding applications.
Please I need to learn the mechanical drawings, especially on this gate valve. Thanks
Thanks Guys,
Your Support are Highly Appreciated in advanced. We go Proactive mode then track Predictive can be more insight for discuss the solution